|
|
|
|
PRE-ENGINEERED BUILDING SYSTEM
|
Simple to construct steel building with each component manufactured at factory, brought to the site and simply assembled and erected to construct the building in the minimum time frame.
Why choose Pre-Engineered Buildings?
- Pre Engineered Buildings are extremely quick and efficient. They have a simple design, are light weight & easy to construct
- Delivery takes an average of 6 to 8 weeks. Thus, both costs & time of erection are minimized
- The erection process is easy, fast, step by step and easy to fabricate
- Outstanding architectural design can be achieved at low cost
- PEBs are flexible and modular and lend themselves easily to future expansion
Primary and Secondary Framing
There are two general types of Structural Components:
- Primary built-up members: Includes Rafter and column and have minimum yield strength of 34.5 KN/sq. cm.
- Secondary members: Includes typical ‘Z’ and ‘T’ sections and have minimum yield strength of 34.5 KN/sq. cm.
There are four basic types of framing system:
- Clear span: Including a beam and a rafter or column.
- Single slope: Showing slope from one end.
- Multi span: With slope from two sides.
- Multi Gable: A combination of two multi span systems.
Pre-Engineered Buildings Applications
In the USA, where the PEB concept was originally conceived during the second half of the last century, nearly 70% of all single storey non-residential construction now utilizes Pre-Engineered Buildings. Applications range from small car parking sheds through 3.5m wide to 100m (+) wide clear span aircraft hangars, low-rise multi-storey buildings. Almost every conceivable building use has been achieved using the Pre-Engineered Buildings approach.
Common applications of PEBS:
- Factory Sheds
- Warehouses
- Hangars
- Workshops
- Power plants
- Fuel and Gas Stations
- Supermarkets
- Airport Terminal Buildings
- Cold Storages
- Retail Showrooms
- Hospitals
- Stadiums
PEB versus Conventional Steel Buildings
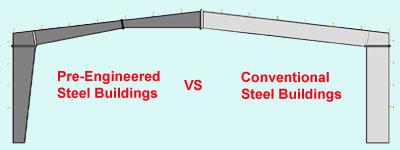
|
Pre-Engineered Buildings (PEB) |
Conventional Steel Buildings |
|
|
|
Design |
Quick and efficient; since PEBs are mainly formed of standard sections and connections, design time is significantly reduced. Basic designs are used ove and over. |
Slow: Each conventional steel structure is desinged from scratch by the Consultant, with fewer design aids available to the Engineer |
Delivery |
Average 6 to 8 weeks |
Average 20 to 26 weeks |
Foundations |
Simple design, easy to construct and light weight. |
Extensive, heavy foundations required. |
Erection Cost & Time |
Both costs & time of erection are minimized. |
Typically, they are 20% more expensive than PEB. In most of the cases, the erection costs and time are not estimated accurately. |
|
The erection process is easy, fast, step by step and with few requirement of equipments. |
Erection is slow and extensive field labor is required. Heavy equipment is often needed. |
Architecture |
Outstanding architectural design can be achieved at low cost using standard architectural features and interface details. |
Special architectural design and features must be developed for each project, which often require research and thus resulting in much highter costs. |
Future Expansion |
PEB Building are designed with future expansion in mind. It is simple, easy and cost effective. One supplier can co-ordinate changes. |
Future expansion would be more difficult and, more likely, costlier. |
Responsibility |
Single responsibility for design, supply and even erection of PEBs. |
Multiple responsibilities can result in questions of who is responsible when components do not fit properly |
View Specification Details 
|
|